商品のご案内
≪ 表面処理 ≫
樹脂上へのメッキプロセス |
Futuron |
The main advantage of the Futuron system is that it eliminates all electroless metal-plating. In the past these steps were indispensable in order to electrodeposit on a non-conductive material. After pretreating and activating the plastic surface, the conventional process used electroless nickel or copper baths. After the electroless layer the electrodeposited layer was applied.
Futuron works without electroless plating steps. Thanks to a major advantage in the process, this eliminates a weak point and a source of faults in plastic electroplating.
【Technology comparison】
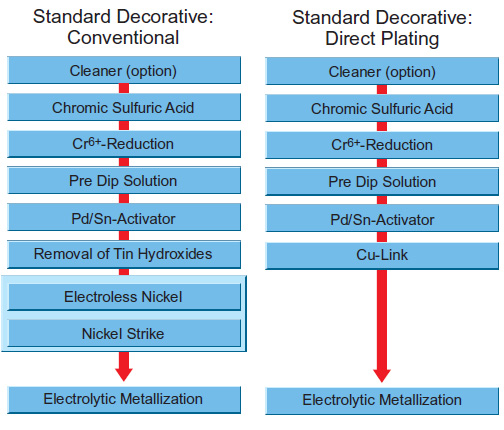
Futuron greatly simplifies the process sequence. The quality of the directly deposited conductive layer is so good that there is no need for the previously required electroless process steps and the subsequent nickel or copper strike.
After pretreatment and activation, the part can be directly electroplated. The acid copper process Futuron Cu ideally complements the Futuron process sequence.
The new technology was developed for plating components on ABS- and ABS/PC Blend-base materials. The process has been adapted to these materials, and thus covers the majority of parts in industrial production.
【Short and sweet: the Futuron process】
A comparison of technologies makes it clear: the new system encompasses just five process steps prior to final electroplating. Up to the point of activation, the process is the same as conventional pretreatment of plastics.
【New developments with Futuron】
- Futuron Cr Additive Solution
- Conditioner C 3
- Futuron Activator Plus
- Futuron Cu-Link Part A Plus
- Futuron Additive H
These products have been developed to improve the cost effectiveness and quality of the Futuron process.
The most important step for achieving adhesive metallization on plastic base materials is an etching solution.
Usually a mixture of chromic acid and sulfuric acid is used. The parameters of this etch bath have to be adjusted to the plastic material in order to get a functionalized and conditioned plastic surface prior to activation.
【Step 2: Chromic acid reduction】
In step 2, Cr6+ is reduced to Cr3+.
This step also protects the entire subsequent process. It is crucial to ensure that no Cr6+ compounds are carried over, as they could negatively influence activation and thus metal-plating, or in extreme cases even prevent metal deposition entirely. Conditioner C3 can be used seperately or in the reducer step (Futuron Reducer Cr + Conditioner C3).
【Step 3: Pre-dip solution】
The pre-dip solution consists of hydrochloric acid whose acid concentration is matched to the subsequent activator.
It protects the activator from dilution.
Therfore no further rinsing between the pre-dip solution and the activator is necessary.
In the activator, palladium and tin are adsorbed on the pretreated surface.
The activator solution contains clusters of tin/palladium alloy encased in tin chloride. The size of these clusters is determined by the concentration of hydrochloric acid and tin, and thus directly influences the quantity of palladium adsorbed on the surface. The goal is to adsorb as much palladium as possible on the plastic surface.
【Step 5: Cu-Link】
While conventional systems remove the protective colloid (tin) from the palladium layer at this stage in the process in order to produce a layer of palladium nuclei on the surface, the Futuron process involves replacing the tin with copper. The solution used for this contains copper ions bound by a biodegradable chelating agent.
The link of copper to the palladium nuclei makes the surface electrically conductive. The resulting conductivity is so good and stable that the surface can then be directly electroplated in an acid copper bath (after rinsing) or the process can be interrupted at this point and the plastic parts dried.
Plating can then be done at a later time with no loss of quality. However, storage conditions should be controlled: the air must be as dry and free from dust as possible.
Additive H function improves the Cu-Link-step. This results in lower Pd-concentration of the Activator.
【The Cupracid family】
Atotech markets a range of highly compatible acid copper systems, the Cupracid family. These highly decorative processes enhance the quality of the finished components. The processes have superb levelling and throwing power and excellent plating distribution.
- Reduced number of process steps means easy integration into existing electroplating equipment
- Shorter process enhances productivity (pretreatment process times are reduced by up to 30%)
- Economical process with less Pd in the Activator
- High production reliability by eliminating electroless nickel or copper baths
- Environment-friendly process. no special waste water treatment is needed
- Resists metal-plating of the racks and prevents unwanted .wild depositing on the rack insulation, only the rack contacts have to be stripped
- The Futuron process has been approved by many major automotive manufacturers in Europe, the USA, and Japan.
Meanwhile direct metallization systems have been included in the latest versions of several automotive specifications. - Companies like DaimlerChrysler, GM, Ford and the Volkswagen Group allow the use of Futuron.
The process is extensively accepted by major sanitary manufacturers like Grohe and Kludi.
【Typical plumbing application schematic description】
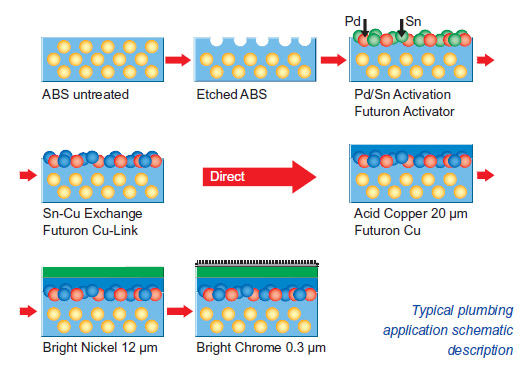